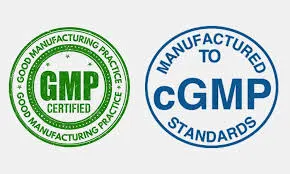
GMP and cGMP Certification
GMP (Good Manufacturing Practice) and cGMP (current Good Manufacturing Practice) are standards and guidelines used in manufacturing processes to ensure that products, particularly in the pharmaceutical, food, cosmetics, and medical device industries, are consistently produced and controlled according to quality standards. The goal is to minimize risks in production processes that cannot be eliminated through testing the final product.
While GMP refers to the general principles and practices for manufacturing processes, cGMP incorporates the latest technologies, practices, and guidelines to ensure the highest quality in manufacturing operations.
Good Manufacturing Practice (GMP) is a system that ensures products are consistently produced and controlled according to the required quality standards. GMP covers all aspects of production, including the raw materials, premises, equipment, training, and personal hygiene of employees involved in manufacturing. The purpose is to ensure that products are safe, effective, and of the highest quality by minimizing errors and inconsistencies during production.
GMP guidelines are essential in industries where product quality and consumer safety are paramount, such as food, pharmaceuticals, cosmetics, and medical devices. Non-compliance with GMP can lead to product recalls, legal consequences, and harm to public health.
- Quality Management: Companies must maintain a quality management system that ensures quality is built into every step of production.
- Sanitation and Hygiene: Manufacturing environments must be clean and sanitary to avoid contamination during production.
- Employee Training: Personnel involved in production processes must be adequately trained in GMP guidelines and quality control procedures.
- Raw Material Control: Only approved and controlled raw materials should be used in the production process.
- Equipment Maintenance: Manufacturing equipment should be regularly inspected, calibrated, and maintained to ensure consistent product quality.
- Documentation and Record Keeping: Detailed records should be maintained for each batch of production to ensure traceability and accountability.
- Corrective Actions: If deviations or non-conformities are found during manufacturing, corrective actions must be implemented to prevent reoccurrence.
cGMP (current Good Manufacturing Practice) refers to the updated and evolving version of GMP. The addition of “current” in cGMP highlights the need for continuous improvement and adaptation to new technologies, methods, and best practices. cGMP ensures that manufacturing processes are flexible enough to adapt to innovations in the industry while maintaining high standards of product quality and safety.
The cGMP system is more dynamic and includes regular updates based on scientific advancements and changes in regulatory requirements. For instance, pharmaceutical companies are required to use up-to-date practices for things like clean room design, computerized control systems, and safety monitoring techniques. cGMP emphasizes the continuous review of processes to keep them in line with the latest practices, improving product quality and safety.
- Adherence to Current Standards: cGMP requires organizations to follow the most up-to-date standards in manufacturing practices. This includes adopting the latest technology and processes to maintain product safety and efficacy.
- Continuous Improvement: Regular review of production processes, equipment, and materials to improve efficiency and prevent quality failures.
- Technology and Automation: The use of automation and digital technologies in monitoring and controlling the manufacturing process.
- Risk Management: Identifying and controlling risks to product quality and safety at every step of the manufacturing process.
- Regulatory Compliance: Ensuring that all aspects of the manufacturing process comply with local and international regulatory requirements, such as those outlined by the U.S. Food and Drug Administration (FDA), the European Medicines Agency (EMA), and other relevant bodies.
The certification process for both GMP and cGMP generally involves several steps, including:
- Pre-Assessment (Optional):
- Organizations may choose to undergo a pre-assessment or gap analysis to evaluate their existing processes against GMP or cGMP standards. This helps to identify areas of improvement before the formal audit.
- Application:
- The company submits an application to an accredited certification body. The application will provide details of the company’s manufacturing practices, procedures, and processes.
- Documentation Review:
- The certification body reviews the organization’s GMP or cGMP documentation, which should include quality manuals, standard operating procedures (SOPs), batch records, and other relevant documents.
- On-Site Audit:
- A certification body conducts an on-site audit of the company’s manufacturing facilities. This audit includes a thorough review of the production processes, employee training, hygiene and safety standards, equipment, and documentation.
- Corrective Actions:
- If non-conformities are found during the audit, the organization must take corrective actions. This could involve adjusting procedures, improving equipment maintenance, or providing additional training to staff.
- Certification Decision:
- After the audit and corrective actions are completed, the certification body will decide whether the company meets GMP or cGMP standards. If the organization is compliant, it is awarded certification.
- Ongoing Surveillance:
- Once certification is granted, the organization is subject to regular surveillance audits to ensure continued compliance with GMP or cGMP requirements. These audits are typically conducted annually or bi-annually.
- Re-Certification:
After a certain period, the organization must undergo a re-certification process to maintain its GMP or cGMP certification. This ensures that the company continues to adhere to the required standards and is keeping up with industry advancements
- Product Quality and Safety:
- Both GMP and cGMP certification ensure that products are manufactured consistently to meet required quality standards. This reduces the risk of contamination, defects, and product recalls, safeguarding consumer health.
- Regulatory Compliance:
- GMP and cGMP certification ensure that the manufacturing processes comply with local and international regulatory requirements. Compliance with these standards is often required to sell products in certain markets.
- Consumer Confidence:
- Certification provides assurance to consumers that the products they purchase are made under safe and controlled conditions, building trust and brand loyalty.
- Market Access:
- Many international markets, especially in the pharmaceutical, food, and cosmetic industries, require GMP or cGMP certification for product imports. Certification opens up access to global markets.
- Risk Management:
- By implementing GMP or cGMP guidelines, companies proactively manage risks associated with product safety and manufacturing processes. This reduces the likelihood of costly recalls or legal issues.
- Operational Efficiency:
- The implementation of GMP or cGMP leads to more efficient manufacturing practices, improved resource utilization, reduced waste, and better product consistency.
- Continuous Improvement:
- cGMP, in particular, emphasizes ongoing updates and improvements to manufacturing processes, ensuring that companies stay up-to-date with new technologies and industry best practices.
GMP and cGMP certification is essential for organizations in industries that manufacture products where quality and safety are critical. These include:
- Pharmaceutical Manufacturers: Companies that produce medicines, vaccines, and other pharmaceutical products need to adhere to GMP/cGMP guidelines to ensure safety, efficacy, and regulatory compliance.
- Food Manufacturers: Food production companies must follow GMP standards to ensure that their products are safe for consumption and free from contaminants.
- Cosmetics Manufacturers: Companies producing cosmetics and personal care products must meet GMP or cGMP standards to ensure consumer safety and compliance with regulatory standards.
- Medical Device Manufacturers: Manufacturers of medical devices must comply with cGMP to ensure the safety and quality of the products they design, manufacture, and distribute.
- Contract Manufacturers: Third-party manufacturers producing products for others must also adhere to GMP/cGMP standards to ensure that the products they produce meet regulatory requirements and safety standards.
Our most Honorable Clients
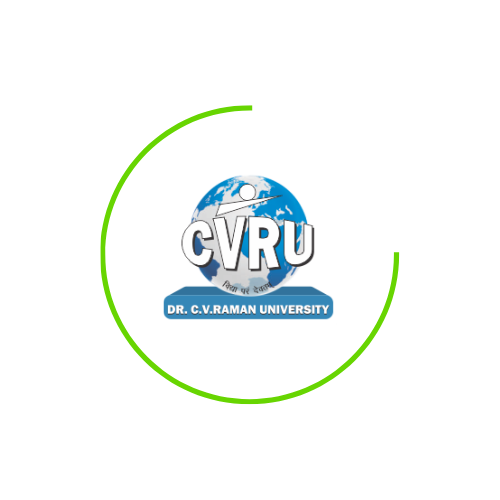
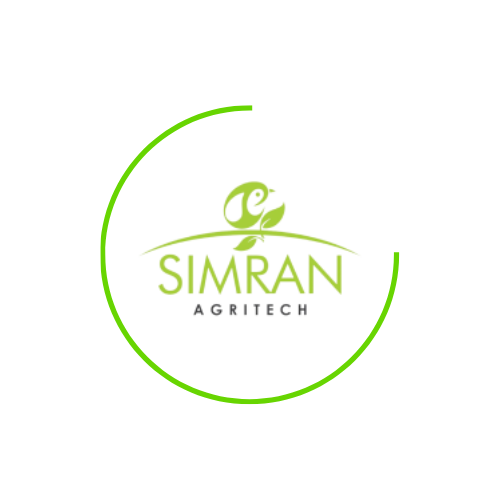
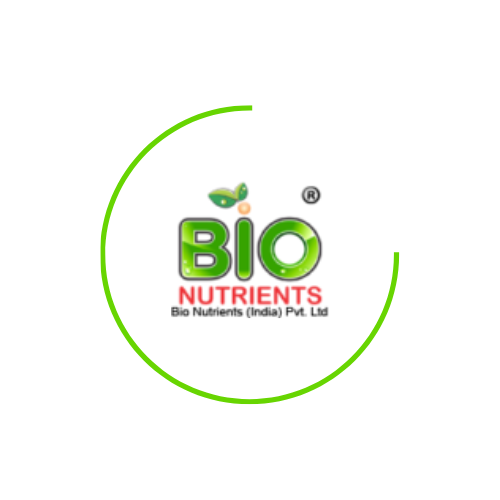
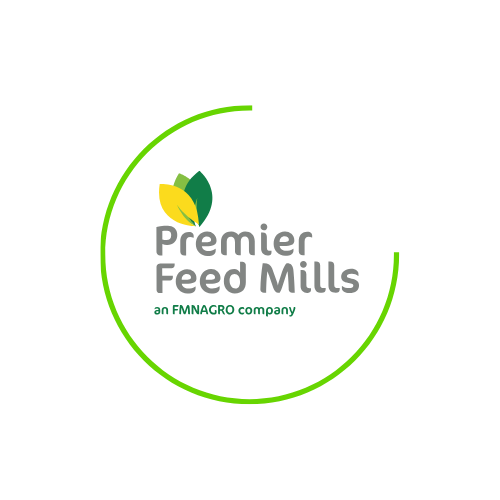
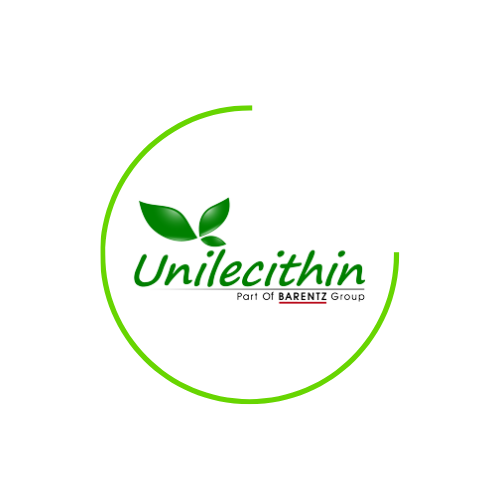
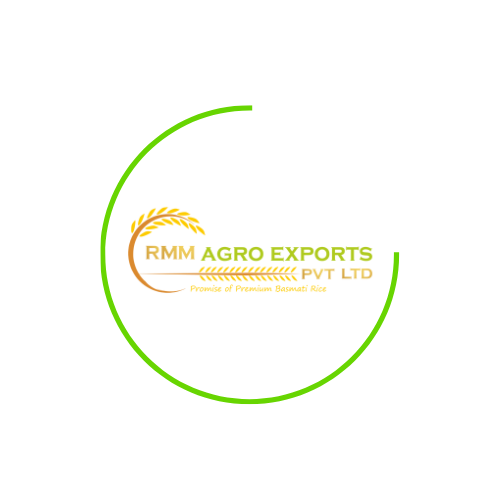

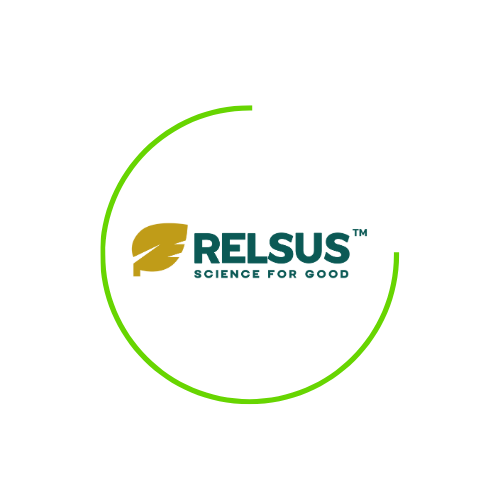
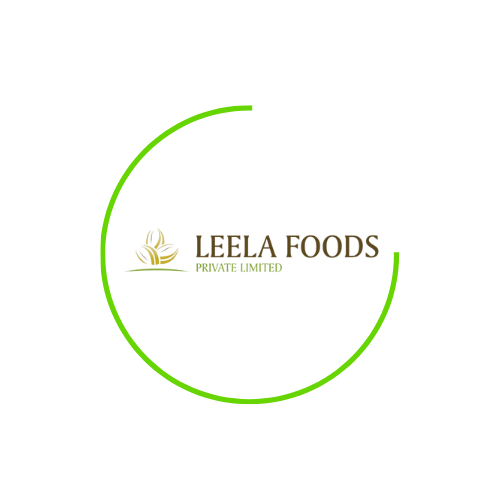
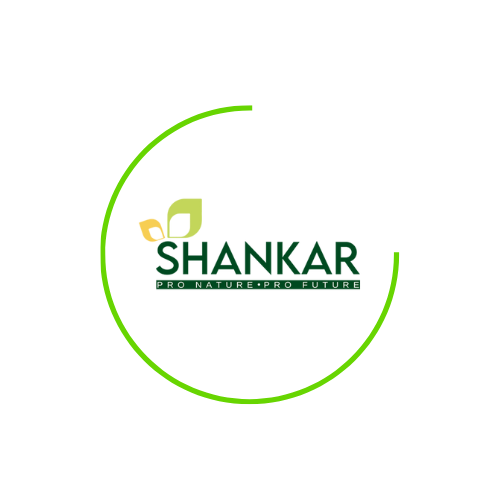
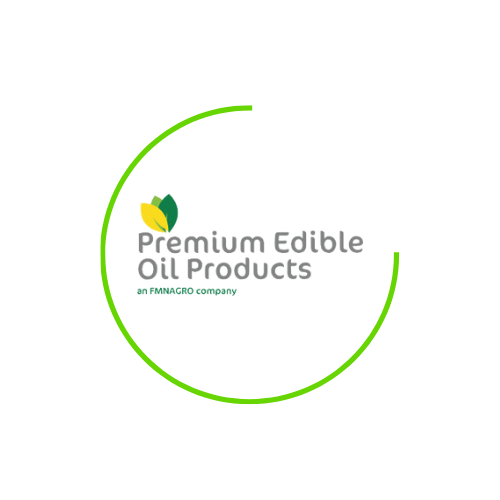
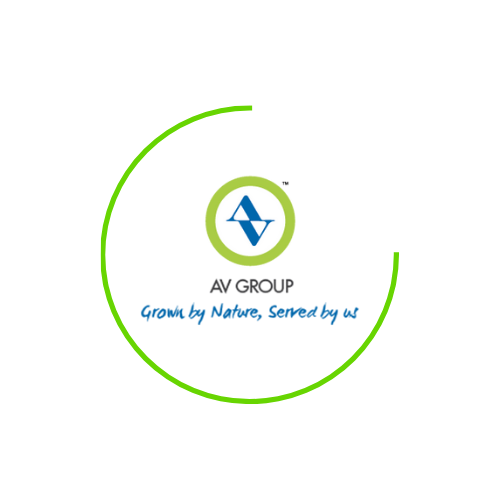
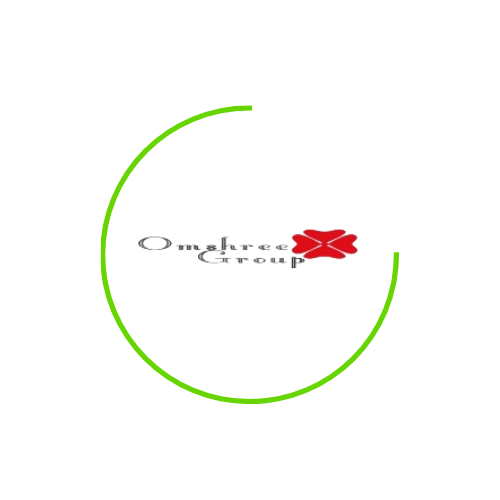
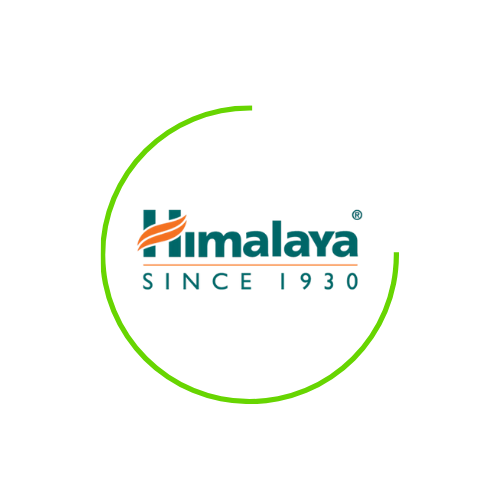
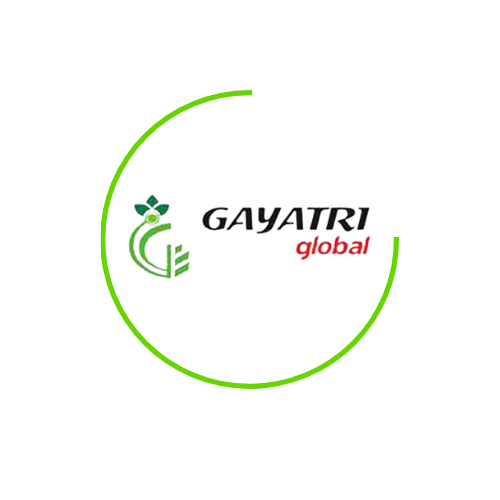
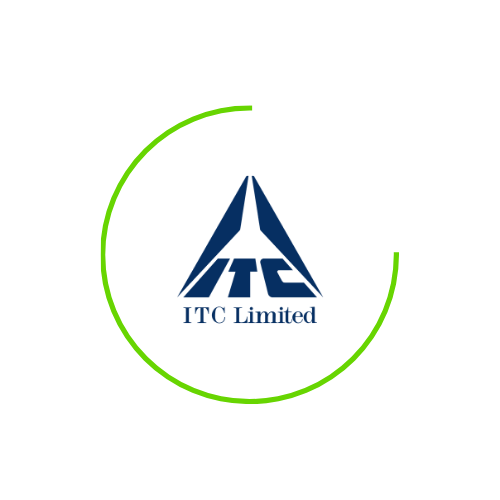
Join Us
Global Certifications
Have questions about our certification process? Need guidance on which certification suits your needs? We’re here to help every step of the way.
Testimonial


